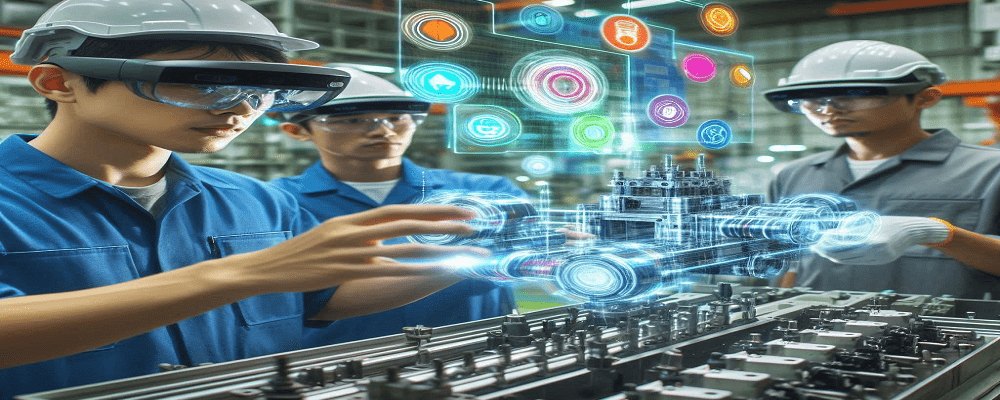
Latest Trends in XR Transforming the Manufacturing Sector
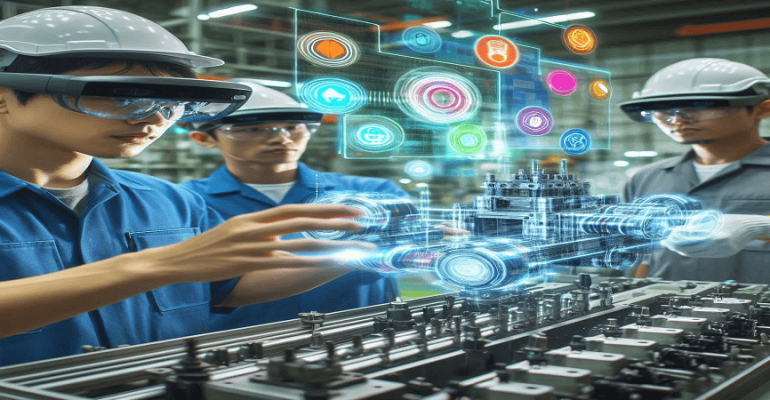
Latest Trends in XR Transforming the Manufacturing Sector
As we move further into 2024, the manufacturing industry continues to evolve rapidly, embracing new technologies to stay competitive. One of the most transformative advancements in recent years is the integration of Extended Reality (XR). XR, encompassing Virtual Reality (VR), Augmented Reality (AR), and Mixed Reality (MR), is revolutionizing manufacturing processes, enhancing productivity, safety, and innovation. Here are the latest trends in XR related to manufacturing:
1. Digital Twins: The Rise of Virtual Replicas
Digital twins are becoming a cornerstone of modern manufacturing. These virtual replicas of physical systems allow manufacturers to monitor, simulate, and optimize their operations in real-time. By leveraging XR, digital twins provide an immersive experience where engineers can interact with and analyze their virtual models. This capability enhances troubleshooting, predictive maintenance, and operational efficiency, ultimately reducing downtime and costs.
Use Case: Siemens employs digital twins in its manufacturing facilities to simulate and predict the impacts of operational changes and external factors on manufacturing systems, significantly reducing downtime and enhancing efficiency.
2. Augmented Reality for Training and Maintenance
AR is making significant strides in improving training and maintenance procedures. Companies like Augment IT and ViewAR are developing AR platforms that facilitate hands-free guidance and remote assistance. Workers can use AR glasses to receive real-time instructions and visual overlays, enhancing their ability to perform complex tasks accurately and efficiently. This not only boosts productivity but also ensures higher safety standards by reducing the likelihood of human error.
Use Case: Boeing uses AR to guide technicians during the assembly of aircraft wire harnesses, leading to a 25% reduction in assembly time and a significant decrease in errors.
3. Enhancing Remote Collaboration
The pandemic accelerated the need for remote collaboration tools, and XR has risen to the challenge. Solutions such as Kognitiv Spark’s RemoteSpark and KIT-AR’s collaboration tools allow remote workers to communicate and collaborate in real-time within a virtual space. These tools are particularly beneficial for quality assurance and remote assistance, enabling experts to provide guidance and support without being physically present.
Use Case: Ford uses VR to enable design teams from different parts of the world to collaborate on vehicle design in real-time, improving the speed and accuracy of the design process
4. Safety and Efficiency Improvements
XR technologies are playing a crucial role in enhancing safety and efficiency in manufacturing. Immersive training environments created using VR allow workers to practice procedures and safety protocols in a controlled, virtual setting. This kind of training reduces the risk of accidents on the factory floor and ensures workers are better prepared for real-world scenarios.
Use Case: Saudi Aramco trains its engineers using VR environments to simulate hazardous scenarios, improving safety training and preparedness without exposing workers to real danger.
5. Workforce Reskilling and Upskilling
As XR technologies become more prevalent, there is a growing need to reskill and upskill the manufacturing workforce. Training programs are increasingly incorporating XR to provide hands-on experience with new tools and technologies. This approach not only enhances digital skills but also fosters a more agile and adaptable workforce capable of handling advanced manufacturing technologies.
Use Case: Lockheed Martin uses AR to train its engineers on assembling spacecraft components, significantly reducing training time and improving assembly accuracy
6. The Industrial Metaverse: A New Frontier
While the initial excitement around the industrial metaverse has subdued, there remains significant interest in using XR to create immersive, interactive manufacturing environments. These environments support activities like design visualization, process simulation, and global collaboration, offering a glimpse into the future of manufacturing.
7. Integration with AI and IoT
XR technologies are increasingly being integrated with Artificial Intelligence (AI) and the Industrial Internet of Things (IIoT). This integration allows for sophisticated data analysis, predictive maintenance, and the creation of smart factories. For instance, XR can visualize data collected from IIoT devices, providing a comprehensive understanding of manufacturing processes and enabling more informed decision-making.
Use Case: GE uses a combination of AR, AI, and IIoT to create a smart factory environment where real-time data from machines is used to predict maintenance needs and optimize production processes
Conclusion
The integration of XR technologies in manufacturing is not just a trend; it’s a paradigm shift that is transforming the industry. From enhancing training and safety to improving efficiency and enabling advanced simulations, XR is paving the way for a more innovative and resilient manufacturing sector. As these technologies continue to evolve, their impact on manufacturing will only grow, driving further advancements and opening new possibilities for the industry. By staying abreast of these trends and embracing XR, manufacturers can position themselves at the forefront of technological innovation, ensuring sustained growth and competitiveness in an increasingly dynamic global market.