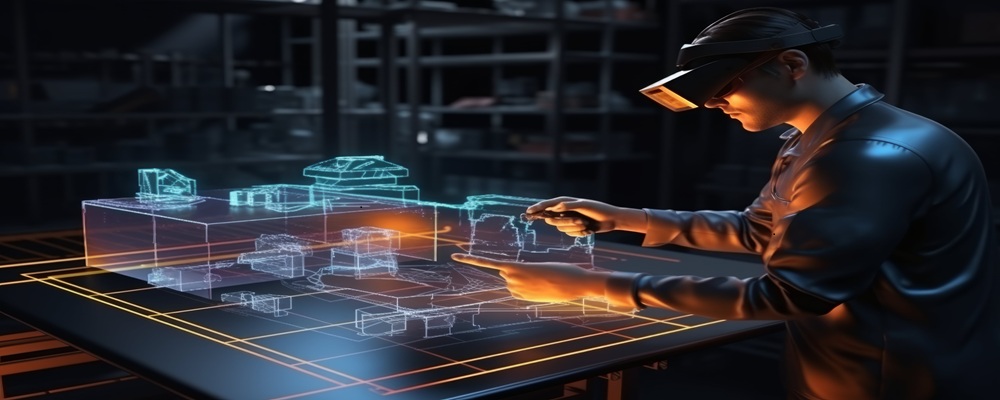
Building Assembly Lines Virtually(XR use cases)
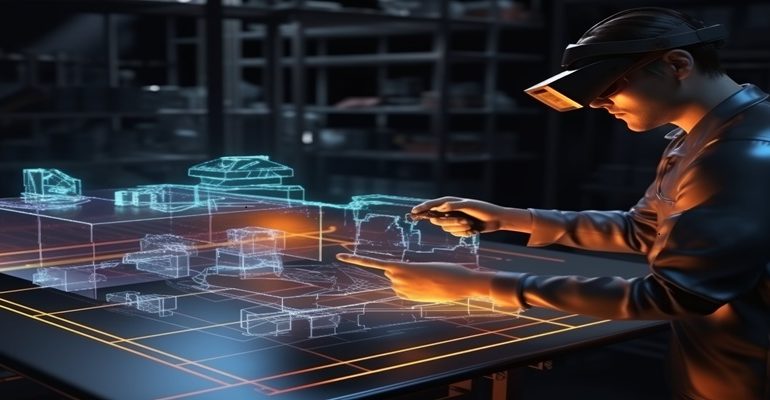
Building Assembly Lines Virtually(XR use cases)
Efficiency is the key to success in the fast-paced world of industrial manufacturing, where downtime is the enemy. What if you could optimize, test, and rebuild your assembly lines without using a wrench? That’s where Extended Reality technology steps in.
Manufacturing approaches for designing and optimization of assembly lines are being completely transformed by XR with remote cooperation and virtual planning to real-time worker training.
Let’s examine how XR-powered virtual assembly lines can revolutionize your manufacturing processes and uncover applications you may not have realized you required.
XR, in assembly line engineering:
- Manufacturers can replicate real-world situations, interactions, and procedures by using XR in immersive environments. When it comes to assembly lines, XR permits:
- Production line digital prototyping.
- Real-time cross-location cooperation.
- AR-guided line configuration and upkeep.
- VR-based instruction for operators.
- XR + IoT for data-driven optimization.
Without interfering with ongoing processes, these advances lead to increased productivity, safety, and time to market.
Problems with the Conventional Assembly Line Configuration:
Prior to discussing XR usage scenarios, let’s look at some common issues that manufacturers face:
- Physical prototyping is expensive and time-consuming.
- Ineffective rearranging of current lines.
- Maintaining safety while educating new operators.
- Insufficient remote cooperation for design verification.
- Downtime when performing maintenance and troubleshooting.
Each of above issues is addressed by XR data-driven solutions.
Use Cases for XR:
1. Design and Simulation of Virtual Assembly Lines:
Using CAD software to design assembly lines is useful but limiting. By enabling engineers to enter a virtual environment and test real-time operations, XR goes one step further.
XR allows you to:
- Before the actual setup, simulate whole assembly lines.
- Test different layouts, combinations, and pathways for handling materials.
- Determine ergonomic hazards and get rid of workflow inefficiencies as soon as possible.
Use Case: A top automaker virtually assessed three-line layouts using XR technology. This resulted in an 18% decrease in worker tiredness and a 22% increase in output – all before any physical changes were made.
2. Cross-Functional Collaboration in a common XR Space:
XR makes cross-location collaboration easier than ever by enabling stakeholders to access a common 3D virtual environment and engage with digital assets in real-time.
Teams can:
- Regardless of location, go over assembly line ideas together.
- Collaboratively annotate, edit, and approve layouts.
- Remove misunderstandings and delays in design reviews.
Use Case: Using our XR remote collaboration platform, a multinational electronics business shortened the assembly design review cycle from 14 days to only 4 days, speeding up project timeframes.
3. Configuring and Reconfiguring AR-Guided Lines:
Augmented reality helps with the actual setup or retooling of assembly lines after the virtual design has been authorized, guaranteeing accuracy and speed.
AR is capable of:
- Instructions for setting up the project in the actual workspace.
- Emphasize the precise locations of the tools and gear.
- Provide error checks and notifications in real time.
- Allow professionals to provide remote guidance.
Use Case: By using AR-guided setup, a heavy-equipment client in Gujarat was able to improve first-time accuracy to 99.5% and reduce reconfiguration time by 30%.
4. Immersive Operator Training in Virtual Reality:
Instead of pausing production to teach personnel on new machinery or SOPs, VR may immerse learners in a safe, digital reproduction of the real world.
Benefits of VR training:
- Risk-free, repeating situations
- Faster onboarding with improved retention
- Performance tracking and feedback dashboards
Use Case: One of our clients, a Tier-1 automotive supplier, cut operator training time from 3 weeks to 5 days utilizing VR training modules designed by Sapizon—without compromising actual operations.
5. Predictive Maintenance and Real-Time Monitoring with XR + IoT:
By integrating XR with IoT systems, manufacturers may visualize equipment health in real-time and undertake predictive maintenance.
This enables:
- Early diagnosis of probable problems
- Live notifications and AR overlays on problematic parts
- Data-backed choices on part replacements
Use Case: A smart appliance maker in Chennai avoided ₹18 lakhs in unexpected downtime by employing our XR + IoT technology to proactively handle machine faults.
Why XR is a Smart Investment for Manufacturers
Extended Reality (XR) has developed from a niche idea into a critical tool for modern manufacturing. Virtually redesigning your assembly lines with XR delivers a wide range of operational and financial benefits.
Here’s how XR provides value to your production process:
Virtual Prototyping:
Create and simulate your complete manufacturing line in a digital environment. Eliminate the need for expensive physical mock-ups and test multiple layouts, workflows, and ergonomic designs before implementation.
Faster Configuration and Setup:
Through AR-guided workflows and immersive visualization, XR facilitates faster installation and changes, greatly cutting down on setup time and related downtime.
Enhanced Operator Training and Safety:
With VR-based training, new hires may rehearse in a safe and realistic virtual setting. This guarantees greater process compliance, speeds up onboarding, and lowers the chance of mishaps.
Inter-Team Real-Time Collaboration:
Cross-functional teams can work together in shared virtual spaces using XR platforms, no matter where they are located. Real-time design evaluations, approvals, and comments help minimize project delays.
Predictive maintenance and insights derived from data:
XR systems offer real-time performance data when paired with IoT, facilitating process optimization and predictive maintenance based on actionable insights.
To sum up, XR is a high-impact investment for long-term growth and operational excellence since it gives producers more speed, precision, flexibility, and intelligence.
How Sapizon Technologies Helps You Implement XR for Assembly Lines
Our expertise at Sapizon Technologies is developing customized XR solution that tackle the particular problem areas faced by manufacturers of heavy machinery, electronics, automotive, and aerospace.
A vast array of customized offerings in XR ecosystem:
- Software for 3D line design and simulation to digitally prototype and improve production processes.
- AR-based setup and troubleshooting apps that provide real-time, detailed instructions to personnel on the ground.
- VR training modules enhance retention and hasten staff onboarding in a risk-free setting.
- XR monitoring platforms with IoT integration that offer useful information on system health and machine performance.
- Solution for remote collaboration where groups from all around the world can jointly design, evaluate, and finalize line configurations.
To provide scalable XR solutions that meet your objectives, KPIs, and industry standards, we collaborate closely with your operations, R&D, and IT teams to make sure that your investment in XR yields quantifiable business results, from strategy and design to deployment and optimization.
Conclusion
A quicker, more intelligent, and more immersive approach to assembly line design, construction, and maintenance is challenging in the conventional ways. Manufacturers can achieve agility, accuracy, and creativity at a scale by digitizing the entire assembly process with XR.
XR can assist you in accomplishing your objectives without the usual risks or delays, whether you’re developing a new production line, retooling an existing one, or upskilling your team.
Our goal at Sapizon Technologies is to support manufacturing companies in implementing XR solutions that provide lasting value and productivity.
Ready to build your XR solution? Schedule a demo with our XR experts now.