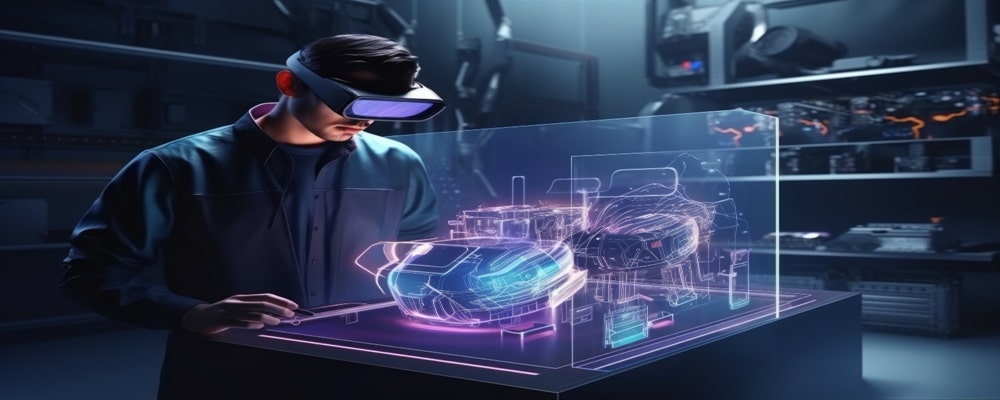
How the Metaverse is Revolutionizing the Manufacturing Industry
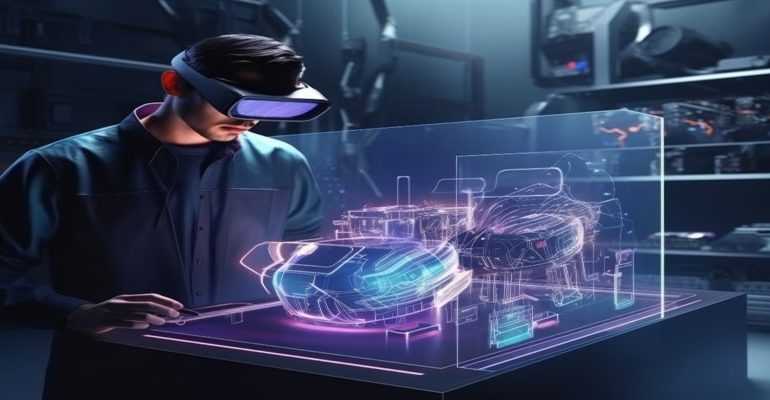
How the Metaverse is Revolutionizing the Manufacturing Industry
The Metaverse—once just a buzzword in the tech world—is rapidly transforming industries beyond gaming and social interaction. One of the most promising areas of impact is the manufacturing industry, where digital innovation is not just an upgrade but a necessity. The integration of Metaverse in manufacturing is reshaping how factories design, test, and produce goods, enhancing efficiency, reducing costs, and enabling smarter decision-making.
What is the Metaverse in the Context of Manufacturing?
The Metaverse in manufacturing refers to a virtual, immersive environment that combines augmented reality (AR), virtual reality (VR), AI, IoT, and digital twins to simulate real-world manufacturing processes. This ecosystem allows companies to build virtual factories, conduct remote operations, train workers, and improve supply chain management in a smart, connected, and scalable way.
Key Benefits of Metaverse in Manufacturing
1. Digital Twin Technology: The Backbone of Smart Manufacturing
One of the most transformative tools in the industrial Metaverse is digital twin technology. A digital twin is a virtual replica of a physical object, system, or process, updated in real-time using IoT data. In manufacturing, this allows engineers to simulate machines, workflows, and even full production lines before physical deployment.
Benefits:
- Predictive maintenance using real-time analytics
- Faster product design iterations
- Enhanced quality control
- Reduced equipment downtime
For example, a digital twin of a robotic arm in a car manufacturing plant can detect misalignments or wear-and-tear before failure, ensuring continuity and efficiency.
2. Virtual Prototyping and Product Design
Traditional prototyping is time-consuming and expensive. Using virtual reality in manufacturing, engineers can create, test, and refine prototypes within the Metaverse environment, significantly reducing the time-to-market.
With real-time collaboration, teams from different locations can interact with the same 3D model, make adjustments, and simulate different product conditions. This leads to faster innovation cycles and reduced design flaws, ultimately saving both time and resources.
3. Immersive Workforce Training
Training workers in high-risk manufacturing environments can be dangerous and costly. The Metaverse offers immersive training simulations using VR headsets, helping employees learn complex machinery operations and safety procedures in a risk-free, interactive environment.
Key outcomes:
- Higher retention of knowledge
- Safe and realistic learning environments
- Reduced onboarding time for new hires
- Scalable training across global teams
This is particularly useful in aerospace, automotive, and heavy equipment manufacturing, where safety is critical.
4. Remote Monitoring and Virtual Factory Tours
Using AR and VR in manufacturing, plant managers can remotely monitor production lines from anywhere in the world. The virtual factory concept enables stakeholders to walk through digital representations of the factory floor, review performance metrics, and detect inefficiencies without being physically present.
This is especially relevant in the post-pandemic remote work environment, where real-time oversight and collaboration need to happen across borders.
5. Enhanced Supply Chain Visibility
The Metaverse in Industry 4.0 facilitates real-time visibility and management of supply chains. Using blockchain and AI integration, manufacturers can track inventory, logistics, and supplier performance in a 3D virtual interface. This reduces bottlenecks, prevents stockouts, and improves supplier accountability.
It also aids in predictive logistics, ensuring that materials and components arrive just in time, supporting lean manufacturing principles.
Use Cases of Metaverse in Manufacturing
· Automotive Industry: Companies like BMW and Ford use digital twins to optimize their production processes and train employees in virtual environments.
- Electronics: Firms are building virtual factories to simulate microchip production and streamline quality control.
- Heavy Machinery: Caterpillar and Komatsu are using AR/VR tools to train operators and perform virtual maintenance checks.
Challenges and Considerations
While the Metaverse in manufacturing offers immense potential, adoption challenges include:
- High initial investment in AR/VR hardware and software
- Need for robust data security and privacy frameworks
- Training the workforce to adopt and use Metaverse technologies
- Integration with legacy systems
However, as technology becomes more affordable and accessible, these barriers are expected to diminish.
Final Thoughts
The future of manufacturing is being shaped by Metaverse, unlocking new levels of productivity, innovation, and collaboration. By adopting digital twin technology, virtual prototyping, and immersive training modules, manufacturers can move toward a smarter, safer, and more efficient production landscape.
For businesses looking to stay competitive in the era of Industry 4.0, embracing the Metaverse for smart manufacturing is no longer optional—it’s essential.