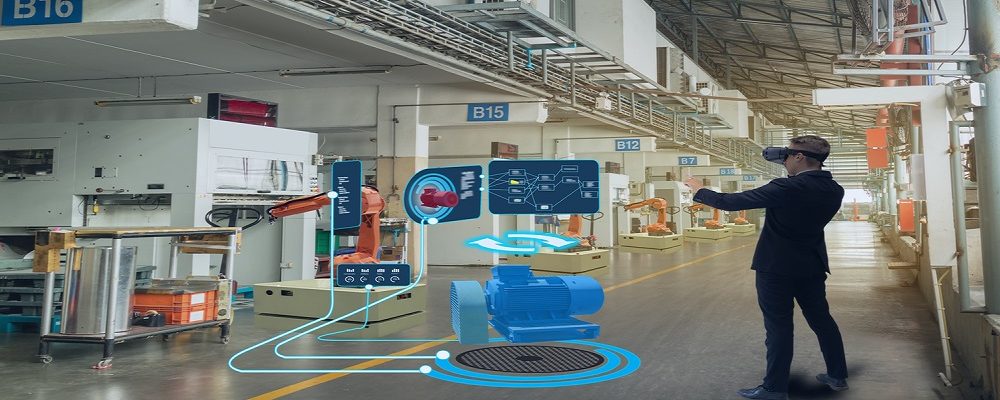
Why Manufacturers Are Dropping Manuals for XR-Based Training
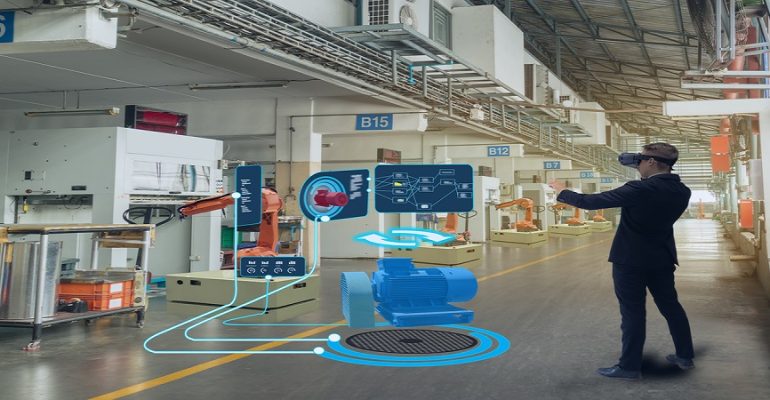
Why Manufacturers Are Dropping Manuals for XR-Based Training
Introduction: Changes in Manufacturing Training
In today’s rapidly changing manufacturing sector, traditional training methods are insufficient. Flipbooks, PDF manuals, and classroom lectures were once the primary methods for onboarding new employees and upskilling existing ones. However, these static, one-size-fits-all processes are no longer sufficient to meet the complexity, speed, and safety standards demanded by modern manufacturing.
Enter Extended Reality (XR), a potent combination of technologies that encompasses Virtual Reality (VR), Augmented Reality (AR), and Mixed Reality (MR). XR is changing the way manufacturers teach their employees, providing a dynamic, immersive, and highly effective replacement to obsolete manuals.
In this blog, we will explore why XR is becoming the new standard in industrial training, how it speeds up onboarding, and why leading manufacturers are investing in immersive simulations to create smarter, safer teams.
What is XR-Based Training?
XR-based training is the use of immersive digital experiences to imitate real-world work situations for training purposes. These simulations allow workers to practice and learn without contacting the actual equipment or procedures.
- VR (Virtual Reality): A fully immersive 3D simulation environment.
- AR (Augmented Reality): The application of digital instructions or graphics to the physical world via smartphones, tablets, or AR glasses.
- MR (Mixed Reality) combines elements of VR and AR, allowing physical and digital objects to interact in real time.
- XR training transforms the learning experience by replacing passive reading and lecture-based approaches with active participation.
Why are Traditional Training Methods failing?
- Despite decades of use, traditional manufacturing training has several drawbacks.
- Low Engagement: Reading manuals or watching videos does not promote hands-on learning.
- Poor Retention: Research indicates that people recall only 10% of what they read and 75% of what they do.
- Long onboarding time: New employees may need weeks or months to properly adjust.
- Safety Risks: Mistakes during real-world training can cause equipment damage or injuries.
- Lack of Standardization: Training quality can vary by location and instructor.
In contrast, XR solutions provide interactive, repeatable, and measurable experiences that enhance both the speed and quality of learning.
Key Advantages of XR Training in Manufacturing
1. Accelerated onboarding
One of the most significant advantages of XR in training is faster onboarding. Instead of relying on printed manuals or shadowing experienced employees, new hires can participate in interactive XR modules that imitate real-world work scenarios.
- Workers can learn by doing things, not simply by seeing them.
- Virtual practice sessions can be repeated until the skills are learned.
- Familiarity with equipment occurs before touching the genuine thing.
- According to a PwC analysis, VR training resulted in 4x faster learning for employees than traditional classroom training.
2. Improved Knowledge Retention
XR offers experiential learning, where users actively engage with content. This results in higher knowledge retention and skill transfer compared to reading or lectures.
For example:
- A worker can virtually assemble a machine part multiple times until it becomes second nature. Mistakes in XR are risk-free, encouraging exploration and deeper learning.
According to research from the National Training Laboratory:
- Reading yields 10% retention.
- Audio-visual training gives 20%.
- Simulation-based training yields up to 75–90% retention
3. Enhanced Safety Training
Manufacturing environments often involve hazardous conditions, from operating heavy machinery to handling chemicals. XR allows workers to practice safety procedures in a controlled, simulated setting.
- Train in emergency procedures without actual risk.
- Identify and correct unsafe practices early.
- Create muscle memory through scenario-based training.
This significantly reduces the number of workplace accidents, especially among new hires.
4. Improved safety training
Manufacturing workplaces frequently have hazardous situations, such as operating heavy machinery and handling chemicals. XR enables workers to practice safety procedures in a safe, simulated environment.
- Prepare for emergencies without putting yourself in danger.
- Early detection and correction of unsafe practices are essential.
- Scenario-based training helps to build muscle memory.
- This significantly reduces workplace accidents, particularly among new employees.
5. Reduced downtime and cost
Physical training necessitates the use of instructors, machinery, and supplies, which frequently results in downtime for production. XR mitigates this by offering:
- Off-site training via virtual reality headgear or augmented reality gadgets.
- Physical assets show no signs of wear or tear.
- Training content is accessible at all times.
While XR development requires an initial cost, the long-term ROI is high because to faster training, fewer errors, and increased productivity.
6. Consistent training in all locations.
Global manufacturers frequently struggle to ensure consistency in training across numerous factories or regions. XR addresses this with standardized digital modules.
- Every employee receives the same high-quality training.
- Local language and regulatory adjustments are simple to apply.
- Data tracking reveals who accomplished what tasks and how effectively they performed.
This eliminates unpredictability and assures conformity throughout your organization.
Real-World Applications of XR Training in Manufacturing
Here’s how XR is used by manufacturers in various sectors:
The automotive industry – Technicians train on assembly lines with VR simulations of specific automobile models. They can practice engine diagnostics and part installation without touching a real vehicle.
Pharmaceutical Manufacturing – Strict protocols and cleanroom procedures can be taught virtually. Workers learn how to maintain sterile environments, prepare compounds, and comply with FDA regulations in virtual reality.
️Heavy equipment – Operators use MR headsets to simulate real-world crane, forklift, and excavator operations. This equips them for real-time coordination and control while avoiding safety risks.
Electronics and semiconductor plants – Complex procedures, such as circuit board assembly and quality testing, are taught using AR overlays, which guide workers step by step with digital instructions.
XR Training vs. Traditional Manuals: A Quick Comparison
Feature | Traditional Manuals | XR-Based Training |
Engagement | Low | High |
Retention | ~10% | 75–90% |
Learning Speed | Slow | Fast |
Safety | Reactive | Proactive & Safe |
Cost | Low upfront, high over time | Medium upfront, low over time |
Scalability | Limited | Highly scalable |
Standardization | Inconsistent | Uniform & repeatable |
Challenges to Consider:
Adopting XR in training presents its own set of challenges:
- Initial investment: Creating high-quality XR modules and purchasing hardware such as VR headsets or AR glasses.
- Content Creation: Modifying modules to reflect actual equipment and workflows.
- Technology Infrastructure: Ensuring compatibility with existing systems (LMS, mobile devices, etc.).
- Resistance to Change: Some employees may require assistance in adapting to new technologies.
However, XR is becoming more inexpensive, and the technology is growing quickly. Early adopters are already seeing significant rewards.
Conclusion
XR is the future of industrial training. As manufacturing becomes more complex and competitive, workforce training must adapt. XR technologies enable manufacturers to create smarter, safer, and more capable teams faster than ever before.
By overcoming the constraints of traditional manuals, XR contributes to the development of a trained workforce prepared for Industry 4.0. Whether it’s increasing production, reducing downtime, or minimizing workplace dangers, XR training adds genuine value to the factory floor.